Extrusion
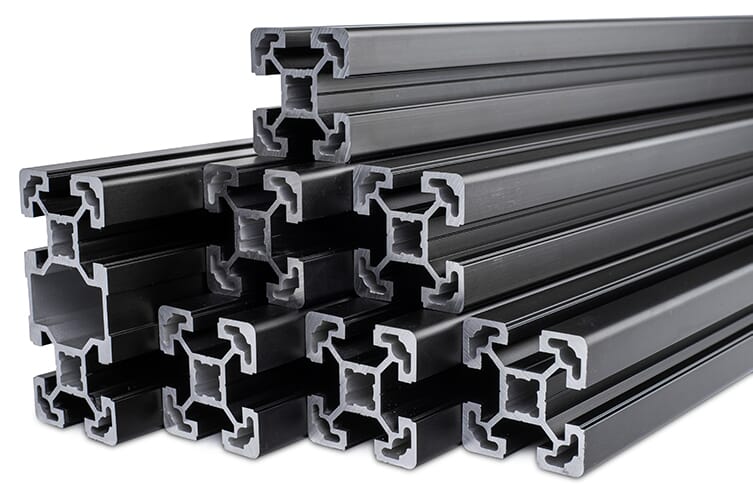
Extrusion
The extrusion process is used to create objects of a fixed, cross-sectional profile. During the extrusion process, a material is extruded (pushed through) a die made to form the desired cross-section.
The process begins by heating the stock material (for hot or warm extrusions). The heated material is then loaded into the container in the press. A dummy block is placed behind the material. A ram then presses against the material to push it through the die. Afterward the extrusion is stretched in order to straighten it. If better properties are required, then the extrusion may be heat treated or cold worked.
The extrusion ratio is defined as the starting cross-sectional area divided by the cross-sectional area of the final extrusion. One of the main advantages of the extrusion process is that this ratio can be very large while still producing quality parts.
Advantages of Extrusion Molding
- Low cost per manufactured part
- Great flexibility of operation
- In hot extrusion, post execution alterations are easier due to product still in the heated condition
- Continuous operation
- Several types of raw materials can be used
- Good mixing (compounding)
- Surface finish obtained is good
- Good mechanical properties obtained in cold extrusion
Materials used for Extrusions
- Aluminum
- Plastic
- Copper
- Rubber