Delivering at the Speed of Light & Overcoming Big Obstacles
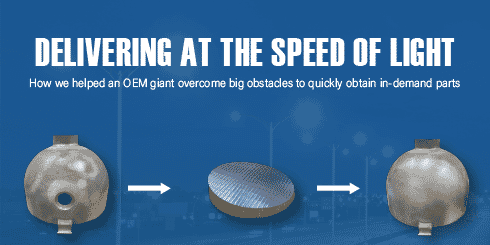

In the world of aluminum die casting, tiny tweaks and small changes are all in a day’s work. Add an engineering change here, a quality inspection there. After all, one of the most-touted benefits of die casting is fast production rates and speeds.
Under normal circumstances, that’s true.
What happens, though, when things aren’t so normal? What happens when there’s a change in unit forecasting and zero units in stock? What happens when the primary overseas supplier is unable to deliver?
If you’re MES, what happens is that you get to work, figuring out how to overcome each and every obstacle to deliver a standout solution.

Jumping the hurdles
“This was a classic example of a high-mix, low-volume situation,” says MES Engineer Steve Crosbie. “Our customer, a world-leader in outdoor lighting, needed an alternate version of one of its 3.3 KG housing units used for exterior commercial lighting. Much like a how solar eye turns on a light, the designs had a single hole to enable similar activation of light. After receiving a significant shipment of the single-hole housings, the customer increased their non-single-hole housing design forecast. That left thousands of single-hole housings sitting in our inventory with zero non-single-hole housings available. We knew we had some decisions make – and fast.”
No-hole, no problem. The supplier can simply reconfigure the tooling then produce the required number of solid, die cast aluminum housing units. Unfortunately, the supplier is located some 20 hours away by plane and, at the time of this project, was on a two-week shutdown celebrating the region’s most significant holiday, Chinese New Year.
That meant the project would require weeks, even months, of lead time. Conservatively speaking, there would need to be a week each for retooling and production, and at least two weeks for expensive, overseas air freight (not to mention the two-week holiday delay).
Charged with figuring out how to cast a mere 1,000 units of this particular housing design – without the help of the regular supplier – meant that MES’s solution had to be swift and seamless.
“We either had to tell our customer there was going to be a two-month lead time,” says Crosbie, “or we could share an innovative, time-saving, cost-beneficial solution. We were committed to sharing the solution. Problem was, we didn’t have one – yet.”
So, Crosbie, along with other MES engineers, brainstormed a range of possibilities before having their lightbulb moment: plug the hole in the housing.

A lightning-quick lighting solution
Though the direction was clear, there were still some obstacles to overcome. Namely, the matter of engineering and manufacturing a plug that would not just cover a hole, but be precisely engineered to fit.
Further complicating the challenge was the housing’s curved profile. To make it work, the plug could not just be round and flat. It had to be designed and machined with a slight camber angle in order to accommodate the housing’s irregular shape and contour.
To create the proper configuration, MES engineers initiated a fundamental problem-solving process: trial and error. With the clock ticking, the team created multiple prototypes with each failed attempt improving the next iteration. Soon, they landed on the exact-right one.
Using an in-house HAAS lathe and mill machine, MES engineers designed, machined, and produced the ideal plug, welding and grinding it until, visually, it disappeared. The end result is a lighting component that looks and functions as a solid unit rather than a patched one. All of which was completed in just a couple days.
Innovation to implementation in a flash
From problem-solving to engineering prototyping to re-configuration to post-manufacturing work, the entire project lasted about the same length as the two-week Chinese New Year celebration.
Thanks to MES’ smart innovation, engineering prowess, and in-house rework capabilities, this commercial lighting provider was able to celebrate both time- and cost-savings while also fulfilling orders on time.
Find out how MES can help solve your biggest obstacles, including post-manufacturing issues. Contact us now.

The MES Solution At-a-Glance
Industry: Commercial Lighting
Company Type: Original Equipment Manufacturing (OEM)
Size/Rank: Fortune 300
Challenge: A leading lighting provider needed a low-volume of solid housing units to meet customer demand. With none available and extra-long lead times on the horizon, our customer was in danger of losing both business revenue and satisfied customers.
Solution: A contoured aluminum plug insert that transformed available single-hole housing units into solid ones with no visible seams.
Results: Our solution not only saved time and money, it allowed our customer to fulfill orders on time while keeping its own customers satisfied.
Metrics:
- 1,000 – Estimated annual units (EAU)
- 2 Weeks – Total turnaround time
- 75% – Time savings
- $ Thousands – Projected cost savings
Services:
- Affordable Aluminum Die Casting
- Post-Manufacturing Engineering
- Customized Rework
- In-house HAAS Lathe & Mill Machining for a Seamless Fit
- Metrics Works Warehouse Order Fulfillment
