5 Ways to Recover from a Major Supply Chain Disruption
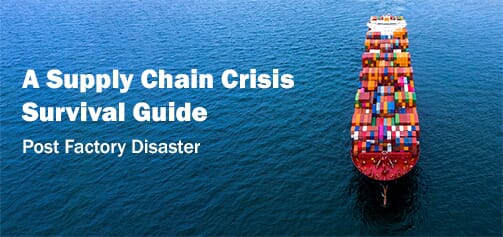
You can’t plan for the unexpected. At least that’s what the global pandemic of 2020/2021 taught us.
Outside of that unprecedented event, most of us in global supply chain management do plan for the unexpected. We have to. It’s called contingency planning for a reason. It’s so we can be ready to proactively respond to anything and everything that has the potential to interrupt our business and impact the manufacturing and flow of goods to our customers.
But what if there’s more to contingency planning than having a “Plan B” emergency response document? What if contingency planning is actually a deep-rooted business strategy designed specifically to build a more resilient supply chain?
That’s the approach our Metrics Ningbo office took just a few weeks ago when facing a governmental shutdown in manufacturing-related activities in the Changzhou region of the Jiangsu province.
Planned Production Delays
The government-mandated shutdown came just before the planned annual Chinese New Year factory shutdown and was a direct result of a tragic dust explosion accident that claimed the lives of 8 workers and injured 8 others.
Facing an unplanned shutdown on top of an already planned shutdown wasn’t exactly how Metrics Ningbo and MES thought the beginning of 2024 would go.
“Traditionally, MES expects a limited workforce at our manufacturing partners for the two weeks before the Chinese New Year along with a slow return to normal staffing and production levels the two weeks after,” explains Eric Turner, MES Director – Global Supply Chain. “So we were headed into the month of February knowing full well that it was highly unlikely we’d see so-called normal production output throughout the entire month of February. We didn’t know there would be a catastrophic explosion, of course. Nor did we know that the government would cease all manufacturing-related activities, including metal manufacturing.”
Manufacturing Shutdowns
There are no words for the devastation experienced by the families, coworkers, and community of those who lost their lives in the Wujin District accident. Naturally, MES understands the decision to shut down production pending an investigation into the accident based, in part, on this statement from authorities:
“There is no trivial matter in production safety … We should learn lessons and receive warnings from various accident cases … It is necessary to find out the crux of the problem … and take resolute and decisive measures … and make every effort to curb the occurrence of various accidents and avoid repeating the same mistakes.”
While a manufacturing shutdown cannot, in any way, be compared to a fatal explosion, the ripple effect of the government halt to manufacturing was felt in this manufacturing-heavy region. Many manufacturers were left in limbo as they awaited governmental inspection and instructions for remediation.
One such manufacturer was one of MES’s closest die casting partners; a partner responsible for 75 of our active part numbers.
In keeping with the government’s response to the explosion, the aftermath impact to our supplier partner was that they were not permitted to resume manufacturing activities weeks later, even after the conclusion of the Chinese New Year holiday.
Assessing the Impact
As we faced a major supply chain disruption, our first course of action was to assess both the immediate and long-term impact. For MES, this involved identifying the extent of the disruption, as well as looking at when inspection and remediation could be expected to conclude so manufacturing could continue.
“Once it was clear that we would not be getting an expedited resolution on the inspection/remediation issue from the local government,” explains Eric, “MES took swift and decisive action to protect our customers’ production lines by ensuring that production could resume ASAP.”
That meant resuming production elsewhere. And for Metrics Ningbo it also meant immediately reaching out to customers to alert them to a potential supply chain disruption.
With those immediate actions done, MES’s boots-on-the-ground team out of the Ningbo office then requested a priority list from the MES Planning team. The priority list gave the team the opportunity to further assess the potential for disruption.
Upon closer inspection, the team determined that there simply was no quick fix that would enable them to make production requirements with the Changzhou supplier.
But, that didn’t stop MES and the Metrics Ningbo teams …
Developing an Action Plan
Putting their heads together, the teams developed an action plan designed to mitigate disruptions and restore our supply chain back to normal as much as possible.
The action plan involved moving both tools and work-in-progress materials from our original die-casting partner to other MES manufacturing partners in the Jiangsu province, as well as to MES suppliers in Ningbo.
The plan was in motion within 48 hours, with two trailers designated for transport of the die cat tooling and one trailer assigned to deliver WIP material to our alternate suppliers.
Collaborating with Partner Suppliers
“Our ability to successfully navigate this manufacturing and supply disruption is due to the hard work and quick thinking of our teams and the strong and resilient supplier partnerships we’ve cultivated,” says MES President Hiten Shah. “Because our core values drive everything we do, even in the midst of a manufacturing crisis and supply chain disruption, we were able to leverage the collaborative partnerships we have with our suppliers, keep the lines of communication open between ourselves and our suppliers, and be wholly transparent with our customers about the status of their orders.”
Realizing the Outcomes
Within 10 days of implementing the action plan, MES had moved 30 critical die casting tools, trim dies, associated machining fixtures, and quality check fixtures, along with more than 30,000 pieces of WIP material to other MES supplier partners.
“This was a highly coordinated effort involving MES supply chain, sourcing, quality, and APQP teams globally,” says Eric. “To ensure that our customers are continually updated on the delivery of their critical parts, we also developed a comprehensive tracking system that’s being shared with all of our internal stakeholders. I couldn’t be more proud of the innovative thinking and hard work of our teams.”
Conclusion
At MES, we always want to do more than “get back to normal” after a major manufacturing or supply disruption. We want to learn from what’s happened and use it to fuel continuous improvement and long-term thinking that strengthens our global manufacturing network and builds a more resilient supply chain. (Read more here for some practical advice on how to shift your supply chain strategy in the face of disruption.)
“We’re used to anticipating potential risks and coming up with new ideas and innovative strategies under pressure,” says Hiten. “It’s one of the reasons our customers in the lighting, transportation, and e-Mobility sectors turn to us for best-in-class manufacturing and engineered supply chain solutions. We foster a work environment that empowers our associates to take calculated yet smart risks, to craft win-win solutions for our customers, and to nurture a network of the best suppliers in the world.”
To learn more about flawless supply chain management—including finding the right supplier—contact us now.