Critical Aspects of Design for Electric Vehicles
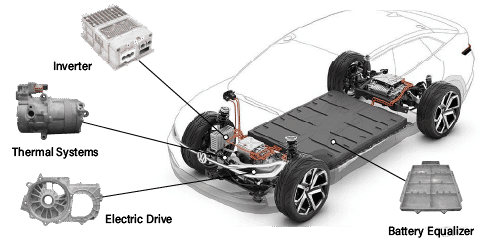

There are incredible options and innovations going on in the EV market. Different companies are going down their unique paths. Companies, large and small, as well as many start-ups, are engaged in Battery technologies, motor technologies, and transmissions. There is a lot of work being done in hydrogen fuel, fuel cell, and other technologies.
MES is doing a lot of work in thermal management and component designs for a variety of applications for electric vehicles. Our study will be presented in several parts as we dig deeper into main assemblies that allow EV development, component designs, benchmark various global EV vehicle designs, and work on R&D for testing methods, material combinations, and design features to help design high performing components.
In this Part 1 of our series, we will highlight the most critical aspects of EV designs. To an engineer working at OEM or Tier 1 supplier, this may seem obvious. Still, to most engineers, buyers, and interested parties, this provides a succinct description of critical components and assemblies in the electric vehicle market.



1) DC Converters: The heart of any EV vehicle is the high voltage battery. It is essential to step down this high voltage current into a 12/24V onboard circuit to power various applications and components in an electric vehicle. DC converters perform this vital function with the smallest mass, volume, highest efficiency, and power.
2) Inverters: Inverters convert the DC power from the batteries into AC power used to operate electric vehicle motors. DC power is fed to the primary winding in a transformer within the inverter housing. Through an electronic switch (generally a set of semiconductor transistors), the direction of the flow of current is continuously and regularly flip-flopped (the electrical charge travels into the primary winding, then abruptly reverses and flows back out0. The in/outflow of electricity produces AC current in the transformer’s secondary winding circuit. Ultimately, this induced alternating current electricity provides power for an AC load for EV motor. The inverter can change the speed at which the motor rotates by adjusting the frequency of the alternating current.
3) Battery Equalizers: The bottleneck for EVs is the high-voltage battery pack, which utilizes most of the space and increases the vehicle’s weight. Currently, the main challenge for the electronics industry is the cell equalization of the battery pack.
Charge equalization for series-connected battery strings has essential ramifications on battery life. Battery equalizers enhance the uniformity of the battery cells and improve the life of the battery as a whole. The basic technique utilizes a simple isolated dc-to-dc converter with a capacitize output filter along with a multi winding transformer. Many OEMs have developed and are continuing to integrate the trickle charge function with the charge equalization function, improving battery efficiency, life, and lower cost implementation instead of frequent battery charging or using more batteries than required.



4) Electric Drives: The drive system is the centerpiece of a battery-electric vehicle. Comprising the power electronics, e-motor, transmission, and battery, the drive system generates zero local CO2 emissions and delivers full torque right from the start. In 2030, one in three vehicles will be a battery-electric vehicle thanks to the electric drive’s steadily improving efficiency and the sinking total cost of ownership for such models.
5) Generator (onboard chargers): Onboard vehicle chargers convert AC energy from the electrical grid to DC energy required to recharge batteries. Battery chargers for plug-in electric vehicles are currently based on proven, traditional, high-frequency charger circuits. They can be located either on the vehicle or off board, as part of a DC fast charger.
AC Power from the charging system is converted into a DC voltage to charge the battery pack using OBCs (On-Board charging systems). OBCs also perform other functions, including charge rate monitoring and protection. Industry charging standards for OBC systems are now developed. Many DC Fast Chargers such as Tesla superchargers plug directly into the quick charging connectors and bypass OBCs. Many large suppliers such as Borg Warner and Eaton are developing different captive versions of OBCs for different OEMs and applications.
6) Power Electronic Controllers: A controller unit is an inverter and converter combination that recharges the battery pack of an EV during regenerative braking, which develops kinetic energy while braking. The flow of energy to and from the battery is controlled using a controller unit in tandem with the Converter-Inverter combinations. Different companies are coming up with a vehicle control module that is adapted to a 24V vehicle applications.
Incredible work is being done to integrate the charging function into existing power electronics and utilize the electric motor’s inductance for recharging. This strategy will lower the part count and reduce the cost, weight, and volume of existing chargers. As with other power electronics, chargers must have a small physical footprint, be lightweight and offer high efficiency and high reliability at low cost.



7) Thermal Systems: Electric vehicle components such as inverters, motors, batteries, battery equalizers, power management, and others use tremendous power and generate a lot of heat. Thermal management entails regulating heat flows inside the vehicle. Components must be operated in their respective optimal temperature range while generating pleasant temperatures for passengers in the vehicle interior. These systems are very complex than in conventional vehicles featuring combustion engines. In an EV, axles must be cooled at all times while the battery needs to be cooled or heated depending upon the respective drive situation.
The refrigerant circuit and the cooling circuit must be optimally coordinated to transport heat inside the vehicle and provide the requisite temperatures. Interconnection of these two circuits changes depending upon the heating or cooling requirements.
8) Battery Pack: The development of battery pack technology has been the single most limiting factor in development and utilization of EV vehicles. Batteries are used to power many high voltage systems such as HVAC and motors and low voltage systems powering various electric vehicle components.
The most common battery type in modern electric vehicles is lithium-ion and lithium-polymer, because of their high energy density compared to their weight. Other types of rechargeable batteries include lead-acid, nickel-cadmium, nickel-metal hydride, and others.
9) Transmissions: Internal combustion engines only generate usable torque and power in a narrow band of engine speeds. To accelerate the vehicle, multispeed transmissions step that down, in varying gear ratios, to keep the engine in its powerband. Keeping the engine in its power band also proves to be the most efficient and durable. Interestingly, electric motor-generators generate 100% of their torque at very low speeds. They also have a wide operating range. At the bottom end, they can go all the way to 0 RPM without stalling. There’s no need to idle, and when you hit the pedal, full power is available. This is the reason electric vehicles do not need a traditional multispeed transmission. Hence, a vehicle like Tesla Model S, is equipped with a single-speed 9.73:1 step-down transmission.