Electrification: Are you missing a critical design element?
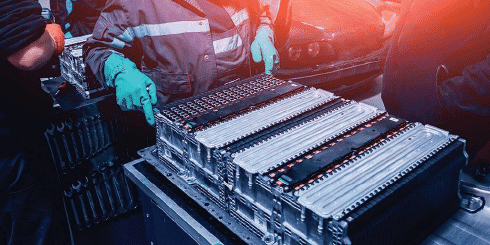
Why it’s important to consider thermal requirements when designing electric vehicle systems?
“What you don’t know can hurt you.”
That quote is attributed to a slew of people ranging from Socrates to motivational speaker Jim Rohn. Regardless of who said it first, though, it might very well be true – at least when it comes to the electrification of transportation.
Between government regulations to help decarbonize the planet to consumer demand for alternative mobility modes, OEMs like you are working fast and furiously to transition to electrification.
Did you know, however, that the future of electric powertrains – your future – brings with it a critical design consideration?
That critical design consideration is this: Thermal management of drivetrain system components.
Why Thermal Management Matters
When it comes to e-mobility, overheating isn’t just a minor concern, it’s a major problem. Because EV market success is contingent on your ability to effectively manage heat in EV batteries, you need a successful thermal management solution.
Here’s why.
Effective thermal designs hold great potential to make a remarkable impact on EVs. They can help:
- Improve component function
- Boost efficiency
- Ensure reliability
- Reduce carbon footprint
- Improve overall vehicle performance
MES Launches Thermal Characteristics Research Program
Because MES wants to help our OEM and other transportation customers, we’ve taken a deep dive into the thermal requirements and design of EV drivetrain systems. How? By launching a research program in collaboration with The Ohio State University (OSU).
Leading the effort at OSU are Professor Ardeshir Contractor and Dr. Navni Verma with support from the Center for High Performance Power Electronics (CHPPE).
This joint program aims to study the thermal characteristics of drivetrain components, such as inverters and batteries with the ultimate goal of developing high-performing components.

Our goal is to drive design changes that result in the development of high-performing components
Phase 1: Studying Real-World Thermal Effects
The first phase of our program was focused on the fabrication of a test rig to enable drive cycle-based loading of EV inverters. This allowed researchers to mimic the thermal effects of real-life operating conditions.
Most EV inverters are liquid-cooled. They use a heat sink on which the inverter modules that house the power-dense, heat-generating insulated gate bipolar transistor (IGBT) switches are mounted. The flow rate and temperature of the liquid coolant is controlled using a pump- and fan-cooled radiator.
Our test rig was developed by senior-year mechanical engineering students as part of their Capstone Project. The team used a BYD-brand sport utility vehicle (SUV) inverter to develop the initial rig design.

Next, the team simulated IGBT heating by using heating elements to generate variable heat for various drive cycles. Combining heat generation with cooling and data-acquisition subsystems, this test rig provided a framework for assessing and comparing various inverter designs, as well as testing improved cooling solutions.
Improving EV Battery Cooling
In conjunction with experimental testing, these OSU researchers also developed high-fidelity, 3D finite element analysis models.
These FEA models simulate the conjugate heat transfer through the compact inverter packaging, helping predict 3D housing temperature distribution.
Researchers are using these physics-based models to enable quick testing of several iterations of potential design features and material combinations to address thermal challenges.

The models help prevent premature, time-consuming, and expensive prototyping and testing while also yielding important data – data that will validate computational models, enhance predictive capabilities, and enable creation of a robust design tool.
Up Next, Phase 2: Enhancing Performance and Reliability
Using this combined experimental and computational framework, researchers anticipate that the next phase of this research project will involve:
- Testing different inverters
- Investigating potential inverter housing improvements
- Exploring heat sink designs to:
- Enrich performance
- Enhance structural reliability
- Reduce component size
Recommendations
At MES, we believe regulating temperatures through evidence-based thermal management solutions will prove to be essential for improving EV performance. So, we’re excited to continue this research to help e-Mobility manufacturers maximize their investment in the electrification of vehicles.
Based on our research to date, we suggest that EV OEMs:
- Visit our blog as we provide updates on our investigation into thermal management solutions.
- Follow the latest ESGC news to stay current with what the U.S. is doing to support advanced technology vehicle manufacturing.
- Keep up with EV laws and incentives.
- Contact us for help in achieving improved fuel efficiency and performance from your EV vehicle components.
As we said, we’ll continue to post here about electrification and thermal management solutions. In the meantime, check out Critical Aspects of Design for Electric Vehicles.