Inverter Research: Using a Test Rig to Improve EV Batteries
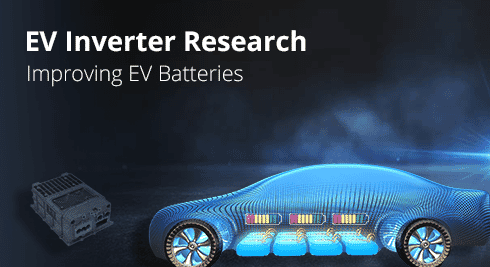
What do a group of student researchers, thermal response, and MES have in common? They’re all part of a relatively new research project focused on the study of thermal management and predictive modeling to develop better EV batteries for the burgeoning e-Mobility market.
This collaboration between MES and researchers at The Ohio State University is well underway, with lots of progress being made in understanding how to create an effective thermal design; something that, of course, automotive OEMs are in need of.
Here’s a look at the latest in this joint research project; this one involving the development and validation of a test rig that can simulate real-world conditions and enable predictive modeling.
How a Test Rig Can Further Next-Gen Inverter Designs
To test state-of-the-art inverter designs and the packaging approaches used to extract heat from power-dense inverter modules, the capstone student team at The Ohio State University constructed an experimental test rig.
When used with an inverter, the test rig emulates drive cycle electrical loading conditions and records the resulting housing temperatures, enabling the team to identify hot spots. The test rig was specifically designed to be interchangeable; that way it can test a variety of inverter housing specimens and designs.
To simulate the real-life operating conditions of an EV inverter, the test rig features three subsystems:
-
- Heat generation: The purpose of this subsystem is to apply a positive heat flux to the housing at the location of the power modules. Each power module consists of transistors and diodes, which are the primary sources of heat in an inverter. In the test rig, this heat generation was emulated using several positive temperature coefficients (PTC) heating elements mounted on the heat sink with thermal paste.
- Closed-loop liquid cooling: This circulates coolant through the heat sink. The test rig was specifically designed to achieve variable flow rates. A radiator and fan remove heat from the coolant, while temperature probes thread into Ts in the coolant system at both the inlet and outlet of the inverter. This provides researchers with a measurement of the temperature difference in the coolant across the heat sink so they can calculate the amount of heat extracted.

3. Data collection: Comprised of surface resistant temperature detectors or RTDs, this measures temperature at critical locations while an infrared (IR) camera maps the temperature distribution of the housing during testing. The RTDs connect to a Data Acquisition System, enabling researchers to access the data on a computer for real-time monitoring and analysis.
Real-World Drive Cycle Simulations
Researchers conducted several tests to demonstrate the capabilities of the test rig. For all of tests, the heating elements were calibrated to dissipate less than 50% of the peak inverter load. Why? To mimic as closely as possible the conditions of city drive cycles.
To study the role of the housing in heat dissipation, the team conducted experiments with and without coolant flow.
Here’s what they found in a series of tests that simulated a car stopped/parked after driving:

Success …
The focus of this capstone was on developing a test rig that can provide repeatable experimental results to generate reliable information for predictive modeling. The test rig was a success!
So, the rig will be used for testing a variety of existing and improved housing designs, which will be informed and verified using FEA simulations.
Be sure to check back for me as we provide additional updates on this project and, more importantly, what impact this could have on the electric vehicle industry.